3 Key Factors That Influence the Cost of Injection Molding
- Plastic Molding MFG
- Jun 2, 2023
- 3 min read
Updated: Apr 4, 2024
Want to spend less to get your product to market? Make sure you understand the most important variables driving injection molding costs.
At Plastic Molding Manufacturing, we have 55 years of experience in plastic manufacturing and engineering. And we're happy to share our knowledge to aid in the development of your application.
Here's a look at the top 3 Key Factors That Influence the Cost of Injection Molding:
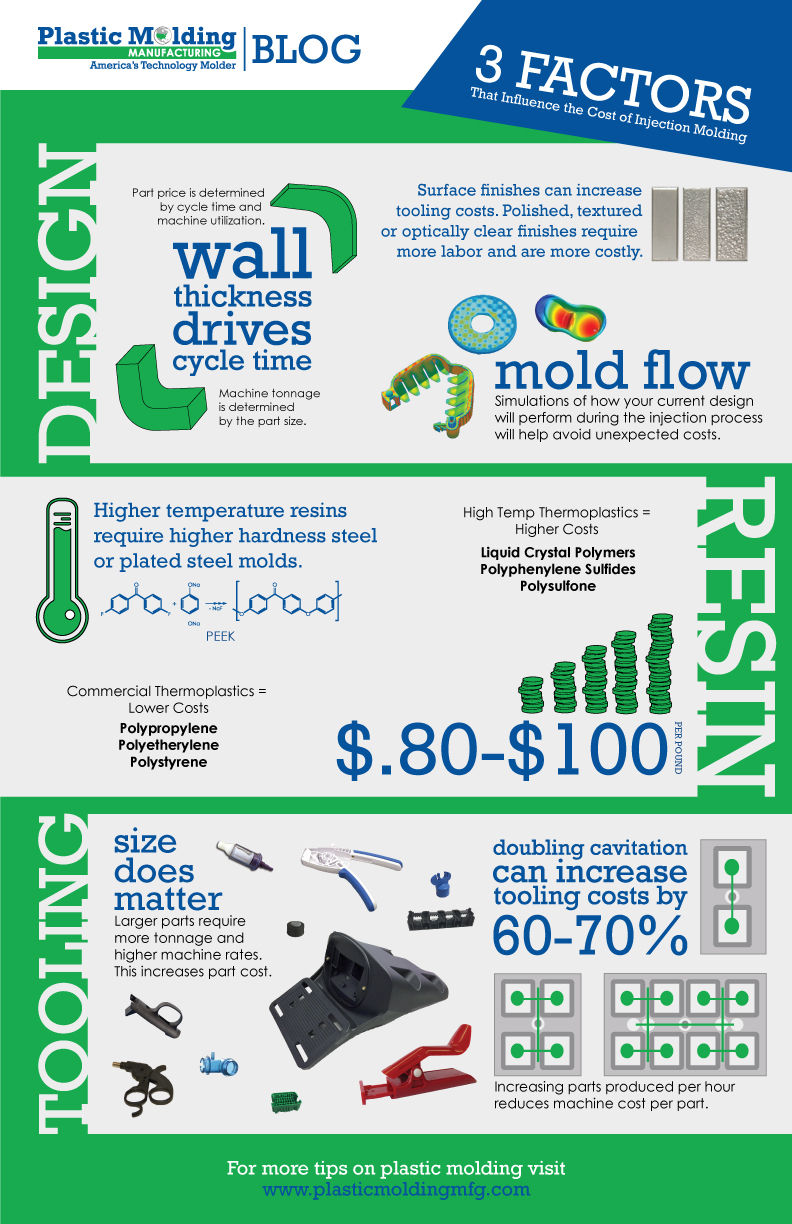
1. Design
Part price is determined largely by two variables: machine use and cycles.
Large parts require more tonnage and higher machine rates than smaller parts. Large molds that call for 300- to 500-ton injection presses require additional setup time. This can boost part price.
Cycle times are determined by wall thickness and part size, which increase machine and material use. Increases in machine and material use can also drive-up part price.
Surface finishes are another factor.
Low-cosmetic finishes are less expensive.
Medium- to high-cosmetic finishes, where tooling marks are removed and the surface is either textured or polished, are more expensive.
High-quality or optically clear finishes are the most expensive due to the additional labor.
Be sure to talk with your plastic engineer about your design. In addition, provide your molding manufacturer with both 3D models and CAD drawings with detailed dimensions and complexity outlined. By having mold flows performed, you can also simulate how your current design will perform during injection molding.
Tip: Avoid unexpected additional tooling costs by performing a design for manufacturability.
2. Resin
Material costs for resin can range anywhere from $0.80 per pound to over $100 per pound. Commodity resins such as polypropylene, polyethylene, and polystyrene are toward the lower end of this range. Polyetheretherketone (PEEK), liquid crystal polymer (LCP), or filled resins with complex properties tend to be more expensive.
Fact: Higher-temperature resins and filled resins require higher Rockwell hardness or plated mold steel, which increase tooling cost.
3. Tooling
Tooling cost is driven primarily by part size and complexity.
Larger parts require larger molds, which tend to take longer to build and qualify (though raising the part capacity can overcome the mold lead time). A higher number of cavities per tool can also increase tooling cost. Doubling cavitation, for instance, can raise tool cost by about 60 to 70 percent.
However, an increase in cavitation also results in more parts produced per hour, effectively reducing machine cost per part. One exception: A mold with more cavities may require a larger press size, thus boosting variable costs (e.g. electricity, setup, space). If the cost of the molding press is amortized in the press rate, a larger press will cost more. Generally, though, the savings from increasing cavitation will outweigh the cost of increasing press size.
Fact: The surface area of a part directly relates to the injection pressure forced on the machine platen. A one-square-inch part requires three to four tons of clamping force.
Tip: Family molds are a great option for lower volumes. A family mold eliminates the cost of purchasing multiple frames for each part. The mold can be designed and built with a runner shutoff so that one part number can run at different times.
A Final Word
The cost of injection molding varies by application. Keep in mind that application design and complexity affect the tooling, machine, and cycles for each part — all of which directly affect mold and part pricing.
Contact our team at sales@plasticmoldingmfg.com or 978-567-1000 for assistant with your plastic applications.